在“雙碳”目標驅動下,水泥行業正經歷著深刻的綠色變革。作為華南地區水泥行業的標桿企業,廣西某水泥集團通過引入創新型技改方案,在水泥粉磨系統節能降耗領域取得突破性進展。通過將傳統鋼段研磨體更換為第三代特種陶瓷球(簡稱:特種陶瓷球,下同),對磨內系統進行全方位有針對性優化改造,該集團水泥旗下二大生產基地3臺水泥粉磨系統不僅實現噸水泥粉磨系統電耗顯著下降,更開創了傳統制造業綠色轉型的典范案例。
科技創新破局,特種陶瓷球技改持續創造節能新高度
2024-2025年間,上述水泥集團先后在柳州二線、三線及融安生產基地實施特種陶瓷球技術改造項目。作為特種陶瓷球技術改造項目方案提供和實施方,新余志宏新材料有限公司針對不同產線的工藝特點,量身定制了包括研磨體級配優化、磨內系統優化升級、預粉磨系統提效等水泥粉磨系統解決方案。
在柳州二線2#水泥粉磨系統改造中,通過優化特種陶瓷球級配方案,在保持原有233.4t/h臺產水平的基礎上,成功將工序電耗從28.33kWh/t降至24.98kWh/t,降幅達11.8%,超額完成合同約定的3kWh/t節能目標。更值得關注的是,在產量零損失的情況下,單月即可節省電能超50萬千瓦時,折合標準煤約60噸,環保效益顯著。
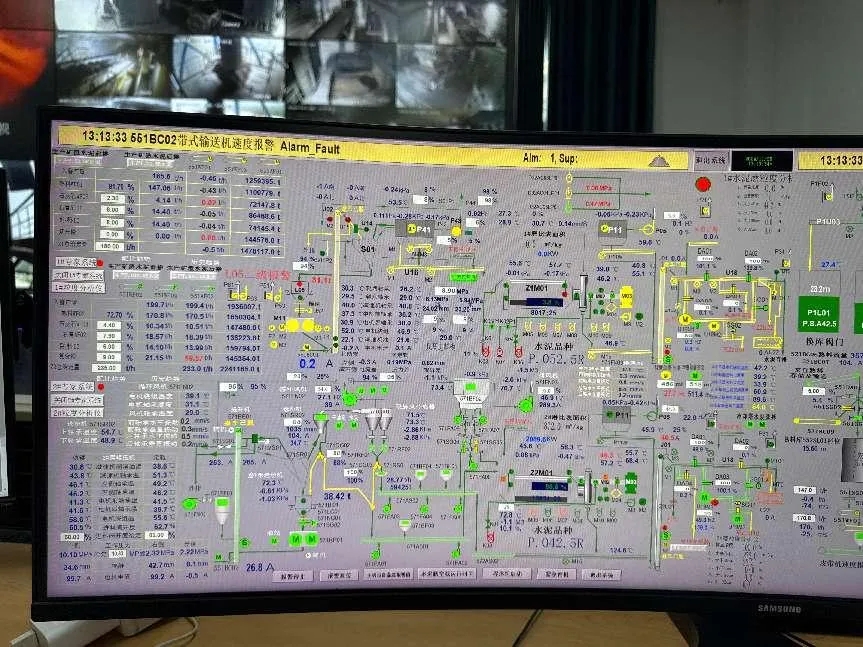
圖:2#水泥磨更換陶瓷球后中控畫面
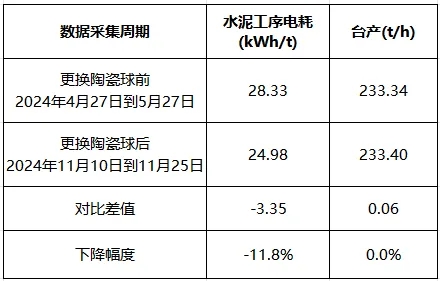
表:2#水泥磨更換特種陶瓷球前后水泥生產數據對比
在柳州三線3#水泥粉磨改造實踐中,項目團隊攻克了特種水泥生產精細化控制難題。通過建立陶瓷球研磨系統的動態調節模型,在臺產基本不降產的基礎上,實現主機系統電耗下降7.1%。這種精準的能耗控制能力,在保持特種水泥品質穩定性的同時,創造了噸水泥綜合成本下降1.2元直接經濟效益。
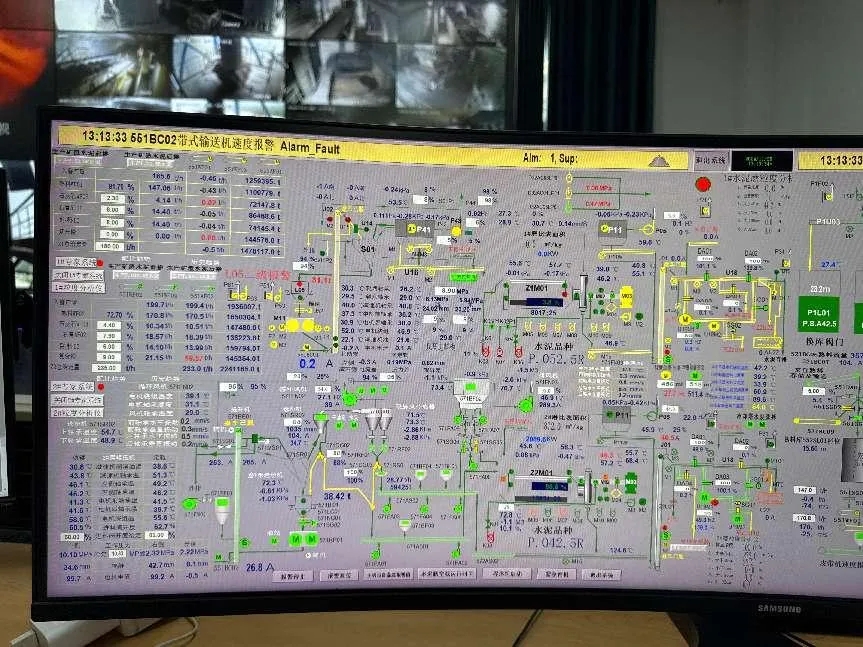
圖:三線3#水泥磨更換陶瓷球后中控畫面
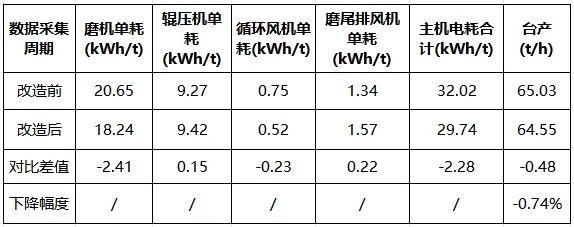
表:三線3#水泥磨更換特種陶瓷球前后水泥生產對比數據
而融安生產基地的改造成果更具行業示范意義。通過采用分段式陶瓷球裝載方案,將二三倉研磨體全數更換為特種陶瓷球后,三大主機設備(磨機、輥壓機、循環風機)綜合電耗降至20.79kWh/t,降幅達13.9%。尤為重要的是,在嚴格控制臺產下降的情況下,通過電耗節約實現單位時間產出效益提升8.6%,充分體現了技改方案的經濟性平衡設計。
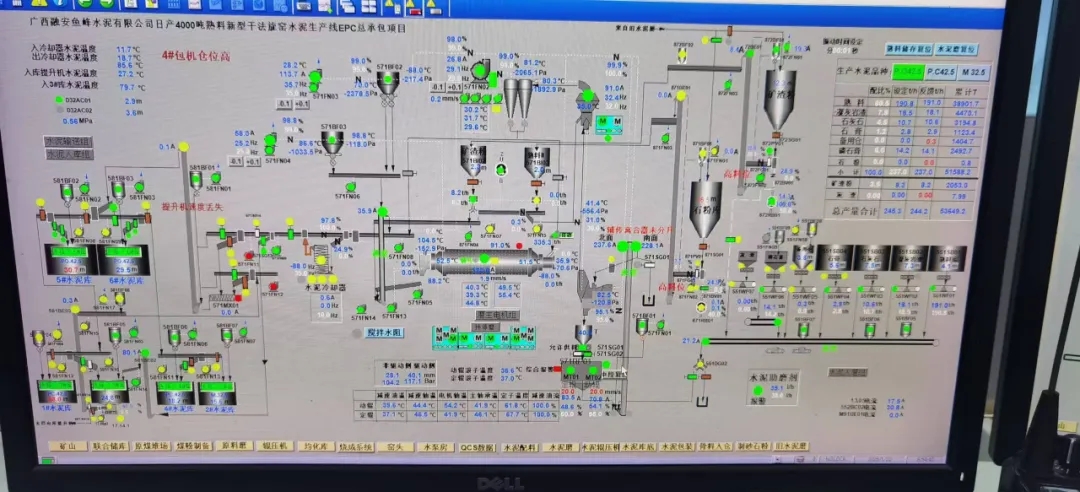
圖:融安生產基地水泥磨更換陶瓷球后中控畫面

表:融安生產基地水泥磨更換特種陶瓷球前后水泥生產對比數據
系統優化賦能:打造系統節能新范式
新余志宏的技改方案遠不止于水泥粉磨系統研磨介質的替代,其核心價值在于構建了“研磨介質替換-運行功率分析-系統優化提效”三位一體的節能體系。項目團隊在企業改造中實時跟蹤特種陶瓷球運行狀態和粉磨系統做功效能數據分析。通過大數據比對和分析,提高水泥粉磨系統運行有效功率占比,降低無效功率占比,采取有針對性優化措施,盡可能降低水泥粉磨系統非必要運行能耗浪費!
在質量控制維度,三個項目均實現產品合格率100%的突破。特種陶瓷球特有低溫研磨特性,將出磨水泥溫度穩定控制在95℃以下,不僅減少冷卻系統能耗,更顯著改善了水泥早期強度穩定性。
這家水泥集團技改實踐驗證了特種陶瓷球技術在水泥粉磨領域的普適價值。從改造效果看,三大項目平均節電率達10.7%,單線年均可減少碳排放超2000噸。這種環保效益與經濟效益的高度統一,為水泥行業落實“能效提升三年行動計劃”提供了可復制和可持續的技術路徑。
新余志宏新材料有限公司技術負責人蘇總對水泥人網表示,我們特種陶瓷球技術解決方案已形成從實驗室研發、驗證到產品實際工業應用完整的產品和技術服務鏈條。我們不滿足于現狀,已瞄準水泥粉磨系統綜合電耗下降20%及以上目標積極努力。當前,該技術已在水泥行業TOP50企業中廣泛應用,累計改造產能突破千萬噸。
在水泥行業超低排放改造的攻堅階段,越來越多的實踐探索證明,通過采取材料創新、工藝優化和產品運用技術服務等系統措施,傳統制造業完全能夠在保持競爭力的同時實現綠色轉型。這種以科技創新驅動能效革命的模式,正在重塑水泥行業的可持續發展格局,為工業領域的“雙碳”目標實現注入強勁動力。